If you have moisture and mold in your home, you’re more likely to have respiratory problems, allergies and weak immune system.When you know the cause of the moisture, you can take steps to limit the moisture in the air.
Likewise, humidity is a natural enemy of filaments.Some materials have no humidity problem.Others, such as PVA or nylon, are very hygroscopic and absorb water after a very short time.The wet filament sizzles and is easy to recognize during printing, and the results are terrible.
Therefore, it is particularly important to store filaments spools carefully and correctly.
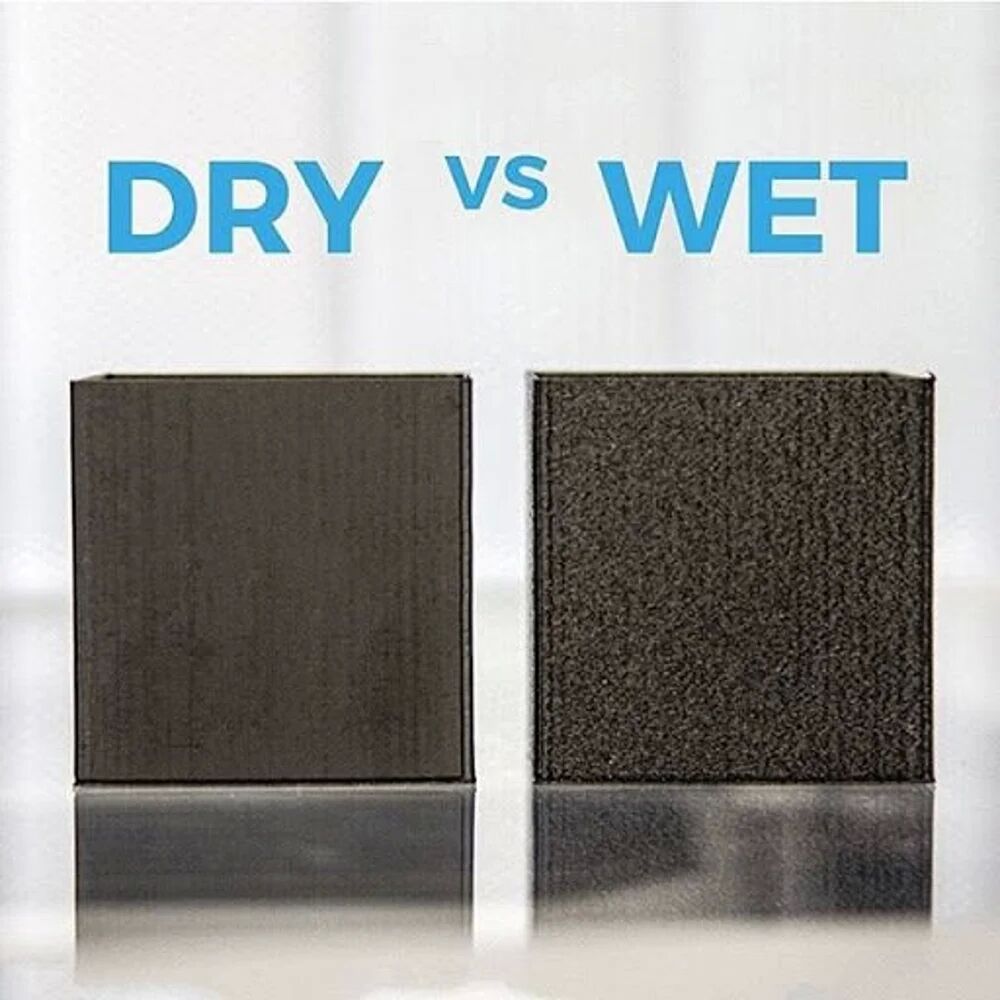
Why Water Damages Thermoplastics
All plastics are polymers or copolymers. you’ll see that the long molecular strands that make up them are woven together when you look at polymers or copolymers under a high-intensity microscope,That means there’s plenty of space between and around the strands.Thererfore, most polymers and copolymers are hygroscopic.Some filament materials, such as Nylon, are very sensitive to water .If they absorb only a little water, they can cause problems when printing.
How To Keep Your 3D Printer Filament Dry
Storing your filament in an airtight container with a desiccant is the easiest way to settle this issue.Filament dry boxes work well, but they can be bulky.
when it comes to airtight,most people think of plastic containers and bags.For the most part, these are good short-term solutions.
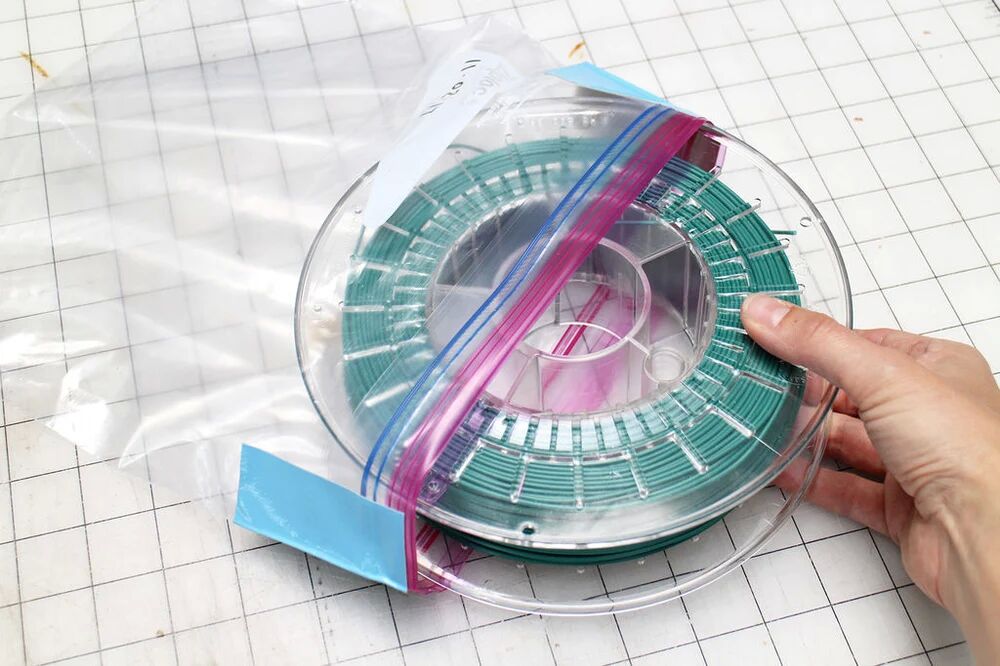
Nevertheless, over time, plastic containers and bags become slightly permeable.This means that the longer your printing materials stay in plastic bags, the more water they absorb, .especially when you live in a humid climate. .If you use a clear bag or box, UV light will also reduce the strength of the filament over time.
Using high-quality Mylar bags or bags made of similar materials is a better solution is to store your thermoplastic.Obviously, there is a layer of metal between two layers of plastic.
This metal layer protects your printing material from any water vapor that permeates the plastic.So that your printing material produces a satisfactory result.


How You Know Your Printing Material Has Absorbed Water
Before printing, there are two simple ways to determine if your material is absorbing water.First, you can measure the diameter of the material itself.when a polymer absorbs water, it begins to grow in size.If the diameter of the filament increases by 10 percent or more, it most likely absorbs water.
Another way to determine whether a filament absorbs water is to extrude a small amount of filament before printing.We’ve all probably been there: sitting by a fire, listening to its crackle.This is because the water in the wood is changed into steam when heated.The same phenomenon occurs when you extrude thermoplastic that has absorbed water.The heat from the print end causes the water in the plastic to expand and escape.You can hear hissing or popping and also see bubbles.
How to Dry Out Filament
If your filament is wet, you must dry it out before using it to print.Why not use an oven?

In the first place, check out the glass transition temperature for the filament that you are going to dry.You need to be sure that you keep your oven temperature below the transition temperature. In a general way , about 60-70C is just about right for most materials, except may be a bit hot for lower temp materials like PLA. Always keep in mind how hot your oven runs and only use electric ovens.
You should also be aware, even if the Glass Transition temp is very high, for a material like Nylon or Polycarbonate – the spool your filament is wound on is likely made from an ABS which will soften at lower temperatures than the filament.
How to dry PLA filament
You ought to be more careful when you dry PLA filament on account that 70C will be too hot. We recommend at the very lowest temp your oven will go around 40C. Even at this temp your PLA will soften, so drying PLA in the oven won’t always give you the results you’re after. It’s a small reminder as to the importance of keeping excellent PLA storage.
Once the oven it up to temperature, place the spooled material inside and leave it there for four to six hours. If you have a convection oven, this drying time may be shortened since the circulated air removes more moisture from the material more quickly.You can also ‘recharge’ the desiccant this way too, placing it in the oven over a low heat.
Once the time is up, remove the material from the oven, allow it to cool and place it into a water impermeable container or bag along with desiccants. Make sure that the container or bag is completely sealed.
Any material that you have oven-dried is slightly more brittle than normal.Remember,Handle the material with care.Only then can you achieve the superior results with your properly dry print material.
Source:
https://all3dp.com/2/filament-spool-8-ways-to-safely-store-your-filament/
https://rigid.ink/blogs/news/how-to-dry-your-filament?_pos=30&_sid=f8cdf3be6&_ss=r